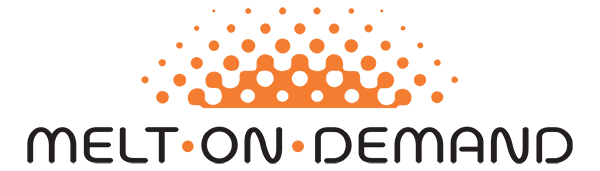
The Evolution of Melt-on-Demand
Char. That was the problem. Char filling hoses, stopping lines, creating ongoing maintenance issues. ITW Dynatec’s customers had a simple, but crucial request: find a way to get rid of the char. And so in the late 1960's, that’s what we did when ITW Dynatec introduced the first melt-on-demand technology.
The very first melt-on-demand technology was called the “No-Char Adhesive Application System”, and was designed to melt on a “first-in, first-out” basis in the absence of oxygen. This consisted of a four stage melt-on-demand process where the adhesive would reach maximum temperature just before the point of application, preventing excess heat from degrading the adhesive in the hopper over time.
Today, melt-on-demand has become the industry standard for reducing char as well as minimizing maintenance and downtime. But, along with the variety of melt-on-demand choices out there, it’s become harder to figure out exactly what is the right solution for every manufacturing line. Even worse, it seems that melt-on-demand has gotten the reputation for offering its benefits only to limited operations, with certain specs, using certain adhesives and so on. The opposite is actually true. Whatever the specifications, the right melt-on-demand solution will always offer you three things: choice, optimization and scalability.
Choice
- Some melt-on-demand systems only work with certain adhesives, limiting your options and potentially putting a strain on your budget, but not all. You can choose a system that works with any adhesive, in any form.
- Tankless systems, which require feeders, are not your only melt-on-demand choice. Feeders are a great idea and reduce the demand on your workforce, but in some cases, floor space is limited and a feeder isn’t an option. In those situations, it’s nice to have a melt-on-demand option that isn’t tankless.
Optimization
- Melt-on-demand systems can deliver staged or progressive melting, depending on your needs.
- Each manufacturing line is unique, and if you choose the right system, you can get a custom-fit melt-on-demand solution to meet your exact specifications, performance need and budget.
Scalability
- Melt-on-demand systems come in varying sizes, so you can choose the ideal size for your operation. There’s no need to struggle with a too-small system or overpay for a too-large system just to take advantage of melt-on-demand.
Today’s Melt-on-Demand
ITW Dynatec exists to create solutions for our customers’ challenges. That’s why we created melt-on-demand technology, and that’s why we keep improving it. Today, using our unique, patented hopper design and following our tested guidelines, you can achieve a char-free system. We guarantee it.